/ ブラスト
ブラストとは 「概要」 と 「メリット・デメリット」
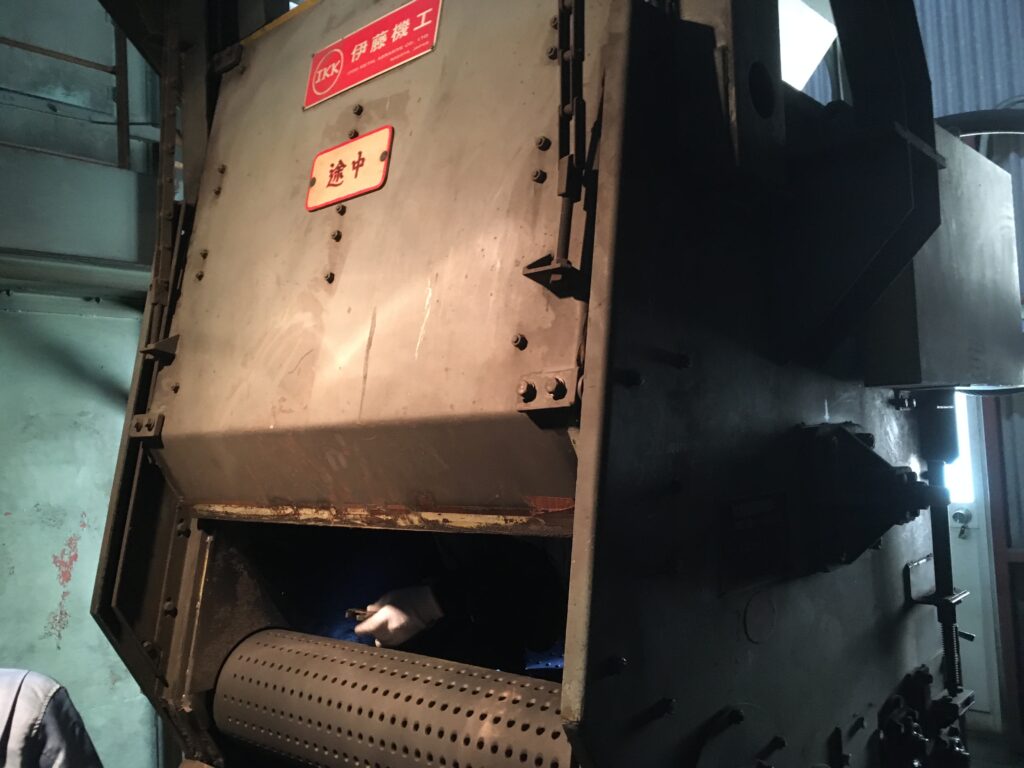
■ブラスト処理とは | ||
ブラスト(Blast)とは「吹き付ける」という意味を持っており、ブラスト処理とは製品の表面に粒子状(砂など)の研磨材を吹き付けし製品表面を加工する処理方法です。研磨材を吹き付けることで、製品の表面を粗らしたり・削ったり・角を取ったりすることができます。ブラスト処理はサンドブラスト・ショットブラストなど複数に分類されており、用途としてはサビ取り・研磨などの目的で使われています。 当ページでは、ブラスト全般について解説します。 |
||
1.ブラスト処理の歴史 | ||
1870年に船舶のサビ取り用として、金剛砂を噴射する装置(サンドブラスト)を、アメリカの技術者ティルマン(B.C.Tilghman)氏が考案したことからブラストの歴史が始まりました。アメリカの非常に風が強い地方で風に運ばれた砂が建物の窓ガラスを削ってしまうところからこの発明に至ったとされています。 このブラスト技術は戦後の日本にも伝わり、当初は工業用途で、船舶のサビ取り・塗装剥がし・下地処理、鋳物の砂落しなどに使用されてきました。その後様々な用途が開発され、近年では回路・IC・電子・電気等の部品・配線加工など数多くの分野で活用されるようになっています。一般的に知られている用途としては、ガラス工芸品の模様付け、墓石の文字入れなどでしょうか。 |
||
2.ブラストの目的 | ||
製品の表面を粗く加工するブラストですが、何のために表面を粗くする必要があるのでしょうか? | ||
01.汚れを落とし見た目を美しくする | ||
表面についたサビや汚れ、塗料などを落とし金属の表面を美しくします。 | ||
02.滑りにくくする | ||
表面を粗すことで凹凸が作られ摩擦がアップし滑りにくくなります。 | ||
03.金属の強度を高める | ||
研磨材などの粒を吹き付ける(叩きつける)ことで、金属の強度を高めてくれます。 | ||
04.金属を長持ちさせる | ||
金属を長持ちさせるためには、サビの進行を防ぐ必要があります。 | ||
その防サビ塗装の密着性を向上させるためにブラストで表面を粗します。 | ||
そうすることで防サビ塗装が剥がれにくくなり金属を長持ちさせることができます。 | ||
3.ブラスト処理の特徴 | ||
研磨材を直接対象物にぶつけて加工するブラスト処理には、以下の特徴があります。 | ||
01.薬品を使用しない加工 | ||
ブラストは処理に薬品などを使用しません。 | ||
ブラスト処理のどの工法も対象物を叩いたり、削ったり、こすったりして効果を発生させる加工のため艶消し状態になりグリップ力が向上します。 | ||
02.一定の加工 | ||
ブラスト処理は投射時の粒子の質量、スピード、形状により決まります。 | ||
粒子が投射された時点で、それ以上の外力が粒子に加わらないため一定の力で加工を行います。 | ||
03.加工面に筋目ができない | ||
ブラスト処理はバフ研磨やラップ研磨のような筋目が発生しません。 | ||
ブラストは粒子が大量に投射されて対象物に衝突することで、対象物の表面には粒子の大きさに合わせた凹凸が大量に形成されます。 | ||
この凹凸は、方向性のない、ランダムな凹凸表面となります。 | ||
04.様々な効果 | ||
ブラスト処理は、粒子の材質やサイズ、形状、衝突スピード、質量などを変えることで、様々な処理効果を得ることができます。 | ||
例えば、多角形の粒子による研削効果や、球形粒子によるピーニングなどが挙げられます。 | ||
05.対象物の材質を選ばない | ||
ブラスト処理は金属、セラミックス、ガラス、石、プラスチック、木材など、さまざまな素材を加工できます。 | ||
ブラスト工法は研磨材を対象物に直接衝突させて加工する工法のため、対象物の材質によらない加工が可能です。 | ||
4.ブラスト処理の用途 | ||
ブラストの工法により違いはありますが、一般的にブラスト工法が利用される用途について説明します。 | ||
〇サビ取り | ||
サビを、薬品を使わず除去できます。 | ||
ブラスト処理は薬剤を使わないので、鉄だけでなく、アルミや銅など、対象の材質に関わらずにサビを除去できます。 | ||
〇フロスト加工 | ||
ガラスなどにブラスト加工を施し、曇りガラスのように白く曇らせる加工方法です。 | ||
〇クリーニング加工 | ||
金属製の部品などの表面をきれいにする加工法です。 | ||
古い塗装の剥離や鋳物などの砂の除去、熱処理後の炭化部分の除去、ダイカスト金型など金属の汚れ落としにもブラスト加工は使われます。 | ||
細かい粒子が隙間に入り込めるため、対象の形状が複雑であっても除去が可能です。 | ||
〇梨地加工 | ||
素材の表面を果物の梨のように加工するブラスト加工です。 | ||
金属や樹脂などの表面に「梨地」と呼ばれる、無数の細かい凹凸を形成することができます。 | ||
アンカー効果(※)による接着力の向上、模様付け、濡れ性の向上などが、この梨地加工の目的となります。 | ||
※塗装・めっきなどにおいて、材料表面の微細な凹凸に接着剤が木の根のように入り込んで硬化することで接着力が高まる効果のこと。 | ||
〇バリ取り | ||
ダイカストや切削、樹脂成型のバリを取り除く加工方法です。 | ||
バリは、製品使用時のケガや品質の低下など、様々な不具合を引きおこします。そのため、必要に応じてブラスト処理によって除去を行います。 | ||
細かな部位のバリも、一定の加工力、方向性がないという特長により、ブラスト処理なら除去可能です。 | ||
〇塗装の剥離 | ||
対象の表面に施された、塗装の剥離に用いられます。 | ||
薬品や熱による処理とは異なり、材質に左右されずに除去が可能なことが特徴です。 | ||
〇酸化スケール除去 | ||
熱処理工程で発生する「黒皮」や、ミルスケールなどとも呼ばれる「酸化スケール」の除去にも用いられます。 | ||
〇WPC処理 | ||
ワンダープロセスクラフトの頭文字を取って、「WPC処理」といいます。 | ||
不二製作所が特許を取得した加工方法で、金属製品の硬さ等を向上させる加工技術です。 | ||
WPC処理を施すことで、ハサミや包丁といった刃物は寿命が伸び、ギアなどの刃欠けが予防できます。 | ||
ゴルフクラブのフェースを加工すると、飛距離が伸びる効果もあるようです。 | ||
〇研磨 | ||
通常のブラスト処理は、対象表面を削り、細かい凹凸を形成します。しかし中には、穴を穿つのではなく、研磨(平滑化)できる処理方式も存在します。 また、この用途に適した特殊な研磨材を使用することで、表面の凹凸を無くし、光沢を持った鏡面にもできます。 |
||
5.ブラスト処理のメリット | ||
01.対象物の材質を選ばない | ||
ブラストは研磨材を衝突させる加工法ため、薬品処理とは違い、対象物の材質を選ばずに加工できます。 | ||
02.加工面に筋目ができない | ||
バフ研磨やラップ研磨などで起こる一定方向へのキズ(筋目)が発生せず、方向性のない凹凸を持つ表面が得られます。 | ||
03.幅広い処理効果 | ||
工法によりますが、同一の装置でも、粒子のサイズや形状、材質、質量などが変わることで、異なる効果が得られます。 | ||
6.ブラスト処理のデメリット | ||
01.処理できるのは研磨材が当たる部分のみ | ||
ブラスト処理は、研磨剤が直接衝突した部分しか加工できません。 | ||
そのため、処理面積の大きさに比例して処理時間が増えること、狭い隙間や筒内面などの処理が難しいことが挙げられます。 | ||
02.機械が摩耗する | ||
研削力の強い研磨材を使用する場合には、対象物の加工と同時に、処理室内や、流路も加工してしまうため、機械自体が削られて摩耗します。 | ||
研磨材の通り道である配管内や投射口などはより加工力が強く摩耗が早いため、定期的な部品の交換が必要になります。 | ||
03.ゴミが蓄積する | ||
加工後の研削くずや破砕した研磨材の破片などが堆積します。 | ||
乾式ブラストの場合にはゴミが粉塵となって発生し、湿式の場合には研磨材の循環使用時に処理品質が不安定になるため、ゴミの廃棄が必要になります。 | ||
7.ブラスト処理の種類 | ||
ブラストは、粒子の使用環境により乾式(ドライ)ブラストと、湿式(ウェット)ブラストの、大きく2つに分けられます。 | ||
また、粒子の加速方法も、機械式とエア式の2つに分類することができます。 | ||
〇ブラスト処理の分類 | ||
![]() |
||
〇サンドブラスト | ||
ドライ/エア式 サンドブラストは、粒子をエア圧で加速して投射するブラスト工法で、一般的にブラストというと、このサンドブラストのことを指す場合が多いです。 加速方式の違いで、「サクション式」と「直圧式」に分けられます。以前は研磨材として砂を使用していたため、「サンド」ブラストと呼ばれていましたが、現在は、アルミナ(酸化アルミニウム)などのセラミックや、ガラス、プラスチック、金属、クルミの粉などを研磨材に用います。 ガラス工芸の模様付けや、墓石の文字入れには、このサンドブラストがよく使われています。 |
||
![]() ![]() |
||
メリット | ||
・様々な粒子を使用できるため、様々な用途に応用できます。 | ||
・圧力調整が容易で、制度の高い処理が行えます。 | ||
デメリット | ||
・処理面に油や水分がある場合は、事前に脱脂や乾燥が必要です。 | ||
・投射される研磨材は容易に舞い散ります。 | ||
〇ブロワブラスト | ||
ドライ/エア式 | ||
研磨材を空気の通路に落として噴射するブラスト工法です。 粒子の噴射・加速にコンプレッサーを使用せず、ブロワと呼ばれる送風機を使用します。ブロワは、コンプレッサーの圧縮エアに比べ低圧で加速が弱く、処理もソフトになりますが、省エネで処理コストも低く抑えられます。 |
||
![]() |
||
メリット | ||
・コンプレッサーが必要なく、省エネで省コストです。 | ||
・ソフトな加工を得意とします | ||
デメリット | ||
・加工力が弱いため、バリ取りや研削など重度の加工が苦手です | ||
・制度の高い加工が困難です | ||
〇ショットブラスト | ||
ドライ/機械式 | ||
モーターで羽根車を回転させ、その遠心力を使って粒子を投射する工法です。 使用される粒子は主に鉄、ステンレス、アルミ、銅などの金属の研磨材が使用されます。広範囲に研磨材が投射されるため、大面積、および、大量処理に利用されます。 |
||
![]() |
||
メリット | ||
・コンプレッサーが必要なく、省エネで省コストです。 | ||
・広範囲に研磨剤を投射するため、大面積の均一処理に向いています。 | ||
デメリット | ||
・加工力の調整が難しく、精度の高い加工が困難です。 | ||
・使用可能な研磨材の種類が少なく、処理が限定されます。 | ||
〇ウェットブラスト | ||
湿式/エア式 | ||
エア圧で水と研磨材の混合液を噴射する、湿式のブラスト工法です。 研磨材が水に混ざっているため、投射時に飛散することが無く、乾式では扱えない、数μm程度の微小粒子まで使用できます。表面の加工と洗浄が同時に行え、乾式に比べて表面への研磨材残りが少ないことが特長です。 |
||
![]() |
||
メリット | ||
・使用可能な研磨材サイズが広く、幅広い加工が可能です。 | ||
・加工と洗浄が同時に行えます。 | ||
デメリット | ||
・濡れてはいけないものを可能出来ません。 | ||
・水に浮かぶ研磨材は使用できません。 | ||
8.まとめ | ||
ブラスト機は単純な構造をしていますが、加工法や研磨材の種類により様々な効果を発揮します。ブラストの特色を理解し、目的に合わせた最適な加工法を選定する必要があります。 | ||